In view of the discovery of petroleum and associated gas in commercial quantities in the Jubilee field in 2007, a National Gas Development Task Force (NGDTF) was constituted by the Government in February 2011 to propose the commercialization of the gas. In April 2011, the recommendation of the task force was approved for the implementation of the Early Phase Gas Infrastructure System (EPGIS) to enable Ghana process raw gas from the Jubilee Field, and the establishment of a national gas entity to oversee the project development and thereafter manage the facility. Ghana National Gas Company (Ghana Gas) was therefore formed and incorporated in July 2011 with a mandate to build, own and operate the natural gas infrastructure required for Gathering, Processing, Transporting and Marketing of the processed gas and derivative products to downstream market.
Ghana Gas was born with a vision “to be a trusted and reliable gas services company” with a mission statement to contribute to Ghana’s Gas economic development by providing and operating the infrastructure required for gathering, processing and delivering natural gas resources, in a safe, cost effective, responsible and reliable manner, to customers.
The EPGIS also referred to as the Western Corridor Gas Infrastructure Development Project (WCGIDP) comprised a:
a. Gas Processing Plant (GPP) of 150mmscd nominal capacity,
b. 58km 12inches offshore gas gathering pipeline,
c. 111km 20inches onshore transmission pipeline from Atuabo to Takoradi (A-T),
d. 75km 20inches onshore transmission pipeline from Esiama to Prestea (E-P),
e. Takoradi Distribution Station (TDS)
The WCGIDP was financed by a loan facility from the China Development Bank and equity funding by the Government of Ghana. The Atuabo GPP and associated facilities were designed and constructed by SINOPEC International. Mechanical completion of the plant was achieved in 2014 and commissioning began on November 10, 2014 whiles commercial operations commenced in April 2015.
In readiness for the Operations and Maintenance (O&M) of these new facilities, Sinopec and Ghana Gas signed an O&M contract for the infrastructure. This was aimed at ensuring Ghana Gas engineers obtained the necessary hands-on knowledge on operating the plant from their Sinopec counterparts.
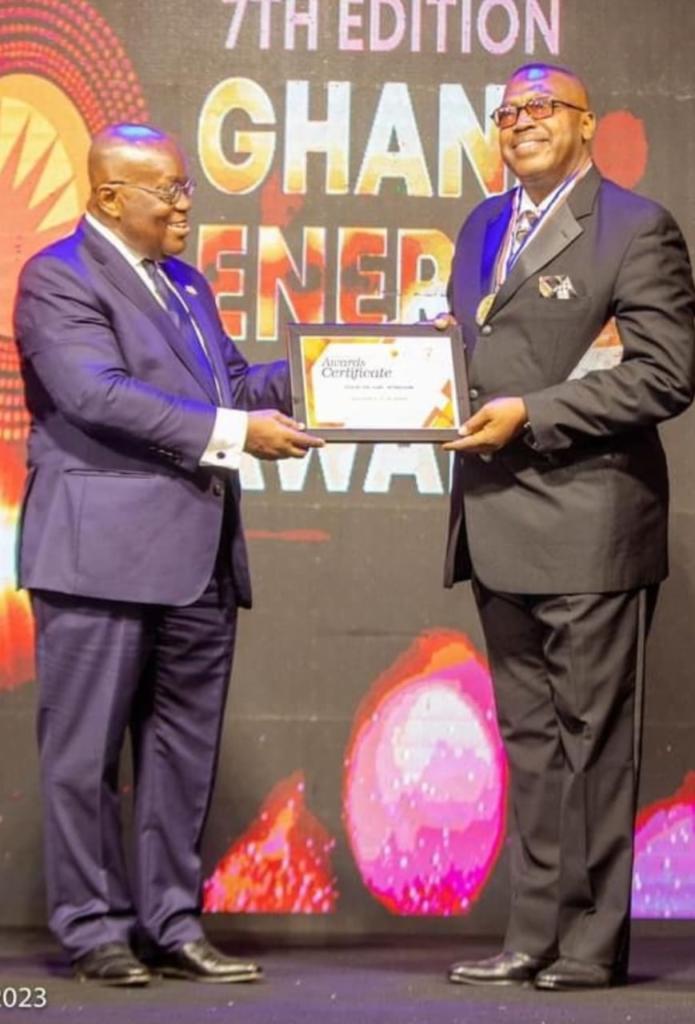
The Road to Indigenization
Gas processing and transmission operations are specialised activities requiring various shades of knowledge in engineering disciplines including: chemical, mechanical, electrical, etc. These engineering disciplines have served as justification for longer term engagement of expatriates to operate and manage the facilities in many resource producing countries. Some oil and gas producing countries have relied on these expatriates for decades and still largely rely on them for efficient operations and maintenance of their gas infrastructure. It has taken some resource rich countries decades and has not yet succeeded in the transfer of the operations and maintenance of such infrastructure to indigenes. To address these issues, some resource countries resort to the enactment and implementation of local content regulations to manage the engagement of expats. These regulations are aimed at ensuring the transfer of knowledge and technology to the locals. For instance, it is took Trinidad 40 years to fully indigenize and Nigeria about 50 years.
Shortly after assuming office as Chief Executive Officer (CEO) of Ghana Gas in 2017, Dr. Ben K.D. Asante, although appreciative of the tremendous work done by their Chinese partners, felt strongly that the time had come for Ghanaian engineers to take up the full operations and maintenance of the installed infrastructure. Thus, he envisioned a gas infrastructure system operating under the full control of competent Ghanaian engineers and technicians.
With strong leadership and commitment, Dr. Ben Asante initiated steps and strategies to enable the Ghanaian engineers to take over the plants fully, thus terminating the O&M contract with Sinopec partners. Relieving the Chinese of their duties implied that there ought to be a deliberate intensification of training and capacity building of the local engineers to give them the needed skill and confidence to run the plant.
As a first step, the CEO, Dr. Ben Asante, who has over 30 years of experience in gas processing and transportation systems and consulted for the company during the construction phase, initiated targeted and tailored training series for the local engineers depending on their strengths and job descriptions. Also critical to the take-over, was to ensure all operating manuals were transcribed into English Language for easy interpretation by operators.
In the first year of the O&M contract, Ghana Gas engineers were required to look over the shoulders of their Sinopec counterparts while they operate and maintained the plant. This went on successfully for the first year, though it came with language barrier issues. By the time the first year contract ended, Ghana Gas’ engineers were ready to take over some utility operations. The second year of the contract was to see Ghana Gas engineers take the driving seats whilst their Chinese counterparts watched and directed. Unfortunately, this was not the case on the ground. Before the second year phased out, Ghana Gas’ engineers had indicated strongly through various fora their ability to successfully take over operations and maintenance of the plant.
In what can be described as a tough decision and yet a legendary one, the new CEO of Ghana Gas on the 1st April, 2017 took a bold decision to entrust operations and maintenance of the early phase gas infrastructure into hands of Ghanaian engineers.
Having achieved a fully Ghanaian manned company, it presented the opportunity to lessen the financial burden that came with hiring the Chinese expatriates and also allowed for some employment of some more Ghanaian workers, thus retaining and spreading the wealth generated from this vast national asset.
Impact of Indigenization
a. Cost Savings/Reduction in Cost
The indigenization of the operations saw the change in hand of the driving seat of all assets owned by GNGC from SINOPEC to locals engineers who had shadowed the Chinese and acquired the expertise in running the installed facilities.
At a point, the company had about 200 Chinese engineers working at the plant site. This translated to a wage bill of approximately USD 3 million in salaries to these foreign counterparts on a monthly basis. This colossal savings in the operational expenditure in the company’s finances provided a huge fiscal space for the company to channel such revenue into other productive and strategic areas of the company.
b. Increased Standard of living
The indigenization drive championed by the CEO of Ghana Gas gave birth to an era of opportunities for the young local engineers in this nascent gas industry to position themselves for greater works. The change also culminated into freeing of space for more manpower (local engineers) to be employed into the company. The increase in local employment meant a transfer of resources control from our foreign partners to indigenes.
The engagement of indigenes in economic activities directly translates to the ability to earn economic gains in the form of salaries and wages. Local engineers formerly unemployed could now afford to support their livelihood and that of their families from the newly provided opportunity, thus good health care, education and meals alike.
c. Socio-Economic Impact
i. Employment – Before the drive of indigenization, GNGC contracted about 200 Chinese to operate and maintained all state installed gas infrastructure. With the advent of the drive coupled with the additions to the installed facilities, GNGC has offered about 1000 jobs to permanent, contracted and casual workers across the length and breadth of Ghana, thus contributing to the reduction of the unemployment rate in Ghana. The company also believes in the use of local contractors for auxiliary services hence additional job creation for Ghanaians.
ii. CSR Projects - The vision of Ghana Gas is supported by three Development Pillars which include Business Development, Personnel or Staff Development and Community Development. The Business Development entails issues relating to the expansion of the operations and revenue management. The Staff Development includes the building and enhancing the competence and intellectual capacity for the personnel for the efficient and sustainable running of the facilities of company. The staff development plays a key role in entrenching the indigenization initiative, as training is considered a constant activity in the company.
Community Development & Engagement, the last development pillar, has improved the development of infrastructure in areas of education, health, sports, water and sanitation in the country. The result of indigenization has saved the company in terms of resources and has made it possible for the portion of the company’s annual revenue to be channelled into community development, for the social – economic development of the country. The corporate objectives of the community development include; maintaining and enhancing congenial working relationships with Project Affected Communities (PACs) and other stakeholders, monitoring, identifying and resolving encroachment issues on the Right of Way (ROW) enhancing grievance resolution mechanism and executing planned CSR projects across the country.
In the Western Region, most importantly the Ellembelle District where Ghana Gas operational facility is situated, several CSR projects have been embarked upon and they include, the construction of a soap making facility and hands-on training centre for GHACOE Women’s Ministry. Construction of Four (4) chamber and half quarters for marine police training, renovation of a two (2) storey girls dormitory at Half Assini Senior High School, modern toilet facility for the Nkroful Agricultural Senior High School, renovation of a residential facilities at Half Assini Government hospital, construction of Mosque and Islamic School at Mpohor.
Ghana Gas has been impactful by ensuring that the education, health and sports needs of Ghanaians are addressed. In the Ashanti Region, the Komfo Anokye Teaching Hospital has seen a construction of a specialist Clinical Center for people to receive special treatment, the renovation of the science laboratory at Kumasi Academy Senior High School, KNUST Senior High has benefited from a multipurpose Laboratory science complex for the students and Presbyterian's hospital at Agogo has seen an installation of an Oxygen Production Plant etc.
Through the Ministry of Education, the company has provided assistance to the Ghana Engineering Scholarship Initiative.
In the Upper West, the company supported the implementation of groundnut, sheep, goat production and Agro-processing projects in Nakori and Chansaa and sponsored the acquisition of standby generator for the Sandema Municipal Hospital in Builsa North and many more projects within the upper west region.
The company has also made an enormous contribution to educational institutions in the country including the University of Mines and Technology (UMAT) study project, KNUST's Engineering Education Project, the Sunyani Technical University Multipurpose Center of Excellence for Electric and Industrial Welding Technology, the University of Science and Natural Resources (UNER).
In areas of sports, the University of Ghana, University of Cape Coast, KNUST and the renovation of the National Hockey Pitch in Accra are the institutions and major sports facilities that have been supported by Ghana Gas to improve upon the sports development of the country. Again, the company has built close to twenty Astro Turfs in the country and this spans across the length and breadth of the country.
Post Indigenization Story
Besides all odds, the company continuous to grow and expand in the pursuit of its mandate as the sole NGTU. This has been made possible by the combination of concerted efforts of all and sundry in the company including the relatively young but hardworking young staff, resilient management led by the visionary CEO and the supportive Board. Upon the development of the five-year strategic corporate plan, under the theme: “Embracing the Future Together: Expanding Infrastructure as an Integrated Gas Entity”. The main objectives of this plan includes to ensure effective internal and external stakeholder engagement, optimize business operations, continuous improvement in business development and sustainable financial growth. The company has chalked lots of successes with these highly motivated young engineers and technicians. Some of these include;
a. Expansion of Infrastructure network:
As the company make strides to expand the gas infrastructure network across the country through projects like the Gas Process Plant Train II, Takoradi-Tema Gas Pipeline project and the Tema-Atiwa-Konongo-Kumasi Gas Pipeline project, other noticeable projects have been completed within the tenure of this management. Ghana Gas completed separate and distinct pipeline interconnection systems for the supply of natural gas to the Karpowership, Twin City Power Plant, Wangkang Ceramics company, Keda Ceramics company, all in the Takoradi environs and Sentuo Ceramics in Tema.
b. Planned Maintenance Shutdowns
As a prudent operator of the gas infrastructure system, we have planned and successful executed three (3) major maintenance shutdowns of the GPP and other stations. This is in line with international best practices and also to ensure the integrity of the plants and systems. Well-seasoned engineers (indigenes) carry out planned maintenance activities to ensure the continuous and sustainable operation of all gas facilities.
c. No-Lost-Time to Injuries
Contrary to misconceptions that indigenisation will impair the efficient operation of the gas plant, pipelines and additional facilities, Ghanaians since taking over the operations of the facilities, has continued commercial processing and transporting of raw gas and derivative products with Zero Lost Time-to-Injury.
d. ISO Certification
ISO 45001:2018 is the new international standard for Occupational Health and Safety management systems published in March 2018. The standard stipulates the framework and requirements for organizations worldwide seeking to benchmark their health and safety management performance to international standards.
After the indigenization of its operations, the management of GNGC strived to adopt safety practices to safeguard the health of its staff and installed assets alike.
In 2022, the company attained the remarkable height of being the first in the energy sector in Ghana to be awarded an ISO45001 certification after several audit of its OH&S management systems by ISO auditors (DNV).
The ISO 45001 certification process has so far enabled the integration of health & safety into the company’s overall business processes at all levels of the organization which is reflected in an increased participation of workers. Through good leadership and commitment of local engineers and auxiliary staff the Certification hangs on the belt of GNGC as one of many to be attained.
Latest Stories
-
GHS takes measures to check Mpox outbreak
42 minutes -
Five dead after tornado tears through St Louis
46 minutes -
Real Madrid confirm Dean Huijsen signing from Bournemouth
1 hour -
Delegates walk out of FIFA congress after Infantino arrives late from Trump trip
1 hour -
Mahama must seek legislative backing for Code of Conduct – Ahiagbah
1 hour -
John-Paul Adjadeh: The visionary behind Ghana’s Premier alumni games
2 hours -
Israel launches major offensive to ‘seize and control’ areas of Gaza
2 hours -
32 youth receive business starter packs from Ghana Grows
2 hours -
NSA Boss visits reptile-breeding Azumah Nelson Youth Centre
2 hours -
It is unfair to blame gov’t for power crisis – Prof Sharif Khalid
2 hours -
Unpredictable cedi appreciation could hurt businesses – Kenneth Thompson warns
2 hours -
Cedi appreciation: We must build reserves that allow long-term predictability – Prof Bopkin
3 hours -
Nine reported killed in Russian strike on civilian bus in Ukraine
3 hours -
Inaction is the main cause of challenge in power sector – Ing. Amissah-Arthur
3 hours -
Ghana’s marine economy: A strategic choice between fishing and coastal tourism
3 hours